ADVANTAGE光工業の強み
お困りごとをご相談ください!
プレス技術で貴社の課題解決に
全力で取り組みます
私たちの技術開発の源泉は、お客様からの「困りごと相談」です。
独りよがりの技術開発ではなく、お客様の課題解決を目的とした技術開発で、
従来は不可能とされていた多くの部品のプレス化・工法置換を実現。
コロンブスの卵的な工法の開発と、創業以来培ってきた金型製作・プレス加工の高い技術力を合わせて、
お客様にダイレクトに貢献してきました。お困りごと、是非ご相談ください。
TECHNOLOGY DEVELOPMENT ABILITY技術開発力
私たちは「開発提案型企業」として、お客様と一緒に製品開発・技術開発を進めています。一般的には不可能と思われている加工や工法置換も、ご相談をいただければ実現に向けて挑戦。これまで蓄積してきた技術ノウハウを存分に活かし、今までにない製造方法を創り出すことに成功しています。
- プレスへの工法置換を全力で考えます
- 大量生産品の安定供給を実現します
- 企画段階からご相談いただければ、より効果的なご提案が可能です
日々進化する、光工業のプレス加工技術
創業50余年の
確かな経験
プレス専業メーカーとして50余年蓄積してきた金型製作とプレス加工技術とノウハウが、新しい技術開発のバックボーンです。
創への挑戦=
チャレンジングスピリッツ
弊社行動指針“創への挑戦”を体現する開発部精鋭部隊が、次の新しい技術を産み出します。
充実した
開発・試作専用設備
”究極のプレス”と称されるULプレスをはじめ、合計5台の開発・試作専用プレスを保有。量産を気にせず開発に専念できる体制が整っています。
プレス加工限界の“16分の1”の加工を実現
- プレス加工では通常、穴と外周間の肉厚は板厚の2倍が必要と言われますが、当製品では穴・外周間の肉厚が板厚の8分の1という特殊加工を実現しました。
- 当製品は厚板であることに加え、スペースの都合から外周部に大きな切欠きが入る設計となっており、8mm板厚に対してこの部分(穴と切欠き部分の間)の肉厚は1mmしか確保できない部品でした。
- 通常は機械加工等を入れないと対応できない加工ですが、当社では独自工法を開発し、プレスとロータリー研磨だけで対応できるようにすることで、従来工法比35%のコスト削減に貢献しました。
- 内径はほぼ全剪断面です(顧客要求は剪断面70%以上)。
- 機械加工でなければ難しい穴導入部のテーパ加工も、プレスで対応しています。
- 内径のR0.25の線ビード(線状突起)3本も、プレス加工で対応しています。
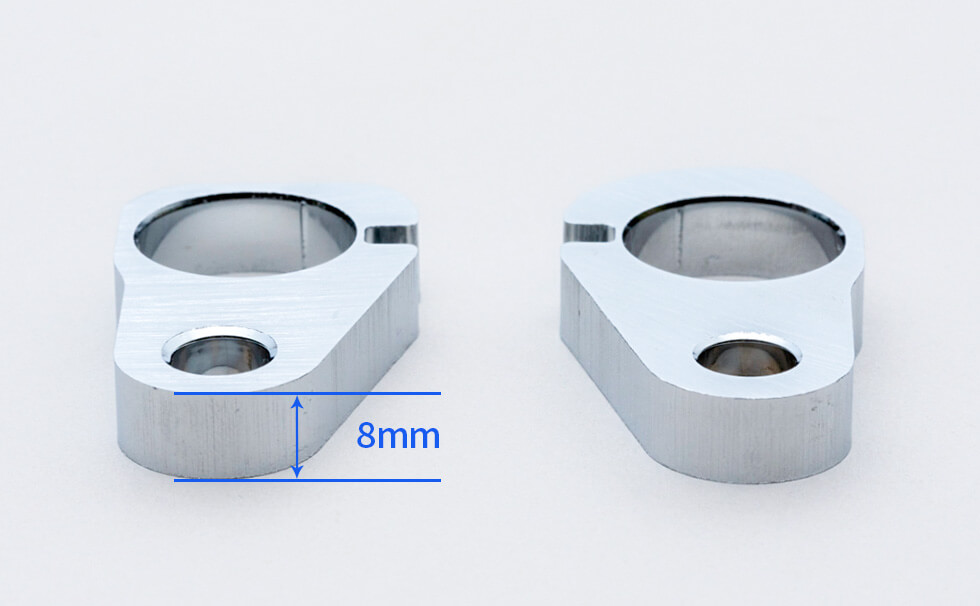
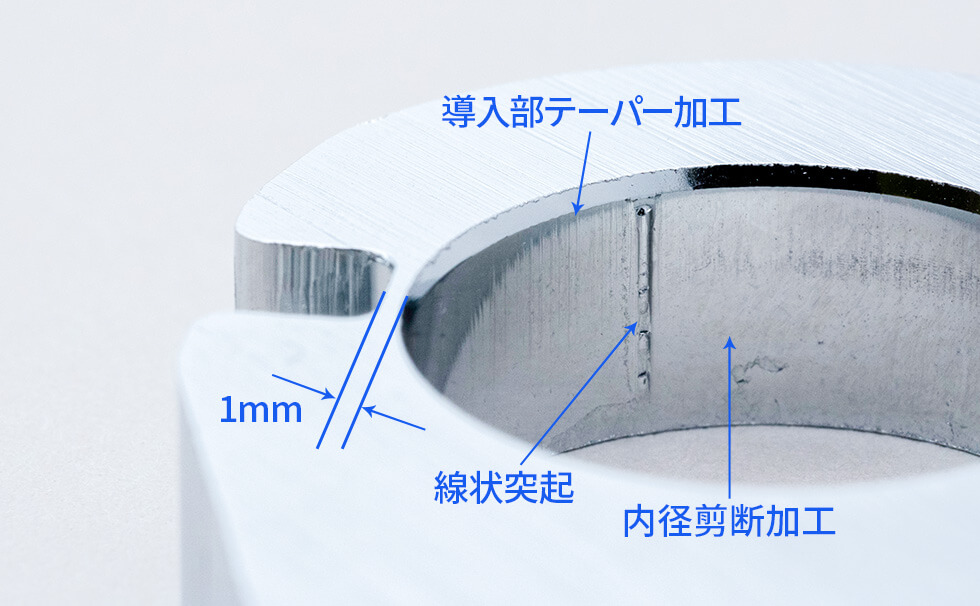
ステンレス厚板フランジのニアネットシェイプ加工
- 当製品は、全剪断加工・内面段付加工・ダレなし加工・塑性流動成形・平面出し加工・バリ極小加工など、これまで培ってきた当社のSUS厚板加工技術の粋を集めた製品です。
- 外周は全剪断状態です。
- SUS厚板としては、ダレを極小に抑えています。
- 穴内面も剪断面が90%を超えています(顧客要求は70%)。
- 穴内面に段付き加工を施しています。
- 塑性流動成形でバーリングを加工しています。
- バリ極小加工で研磨しろを最小限にしています。
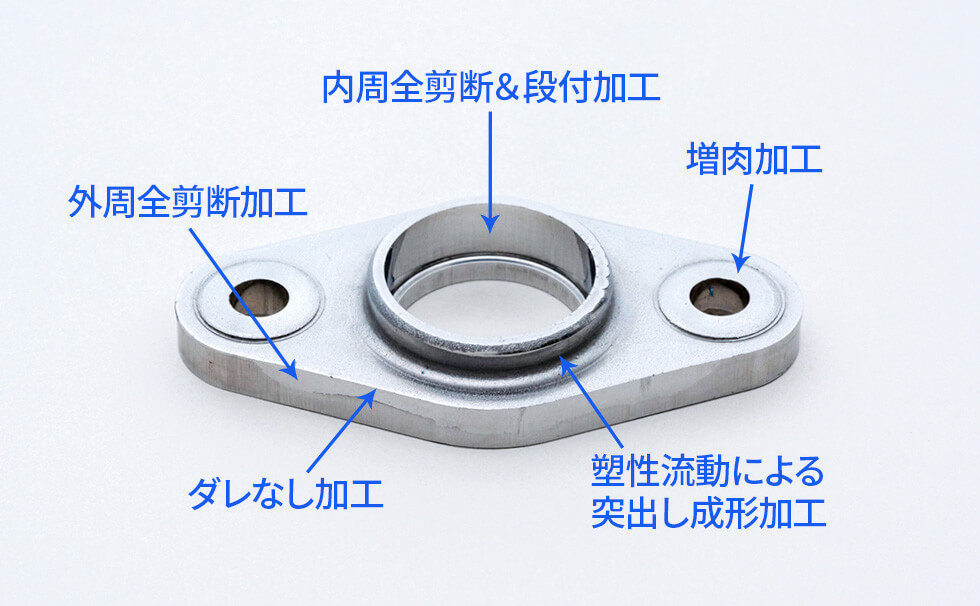
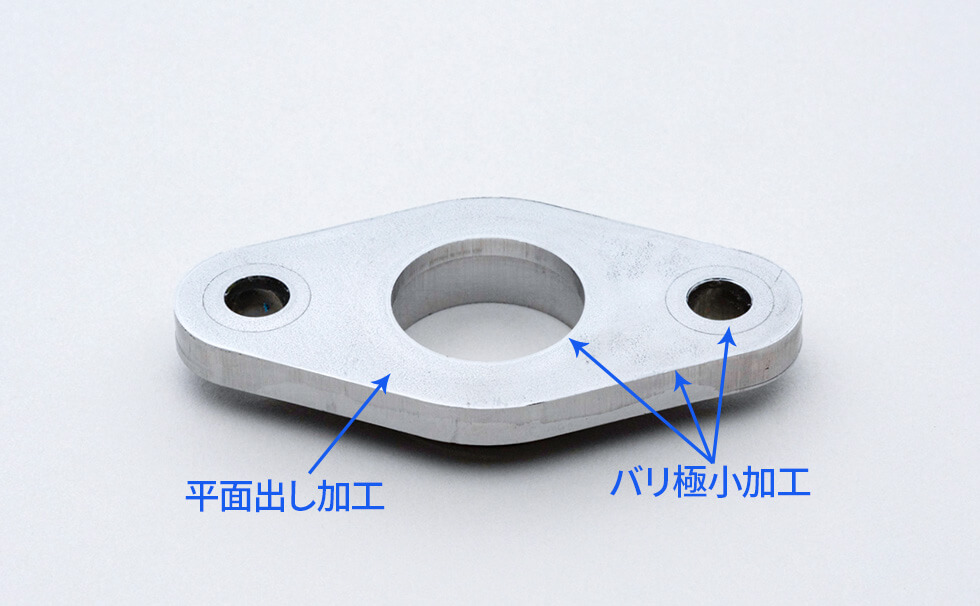
FACILITY積極的な設備投資
新しい技術のための投資を惜しみません
安定的な量産だけでなく、加工精度や品質保証においても、お客様から求められるレベルは年々向上しています。それらの期待に応えるためには、技術の向上はもちろん、最新の設備も重要です。求められる精度を満たすため、お客様が望む新しいことにチャレンジするため、直接製品を産み出すプレス機はもちろん、製品を産み出す治具である金型の生産設備に対しても積極的な投資を行い、充実のラインナップを実現しています。
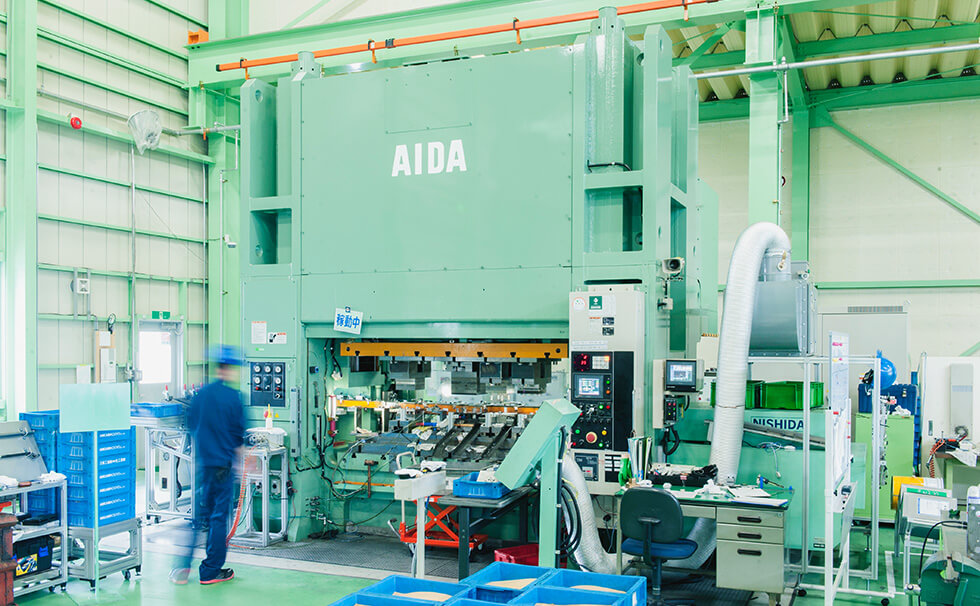
アルティメート精密成形(UL)プレス
(アイダエンジニアリング)

5軸制御マシニングセンター(安田工業)
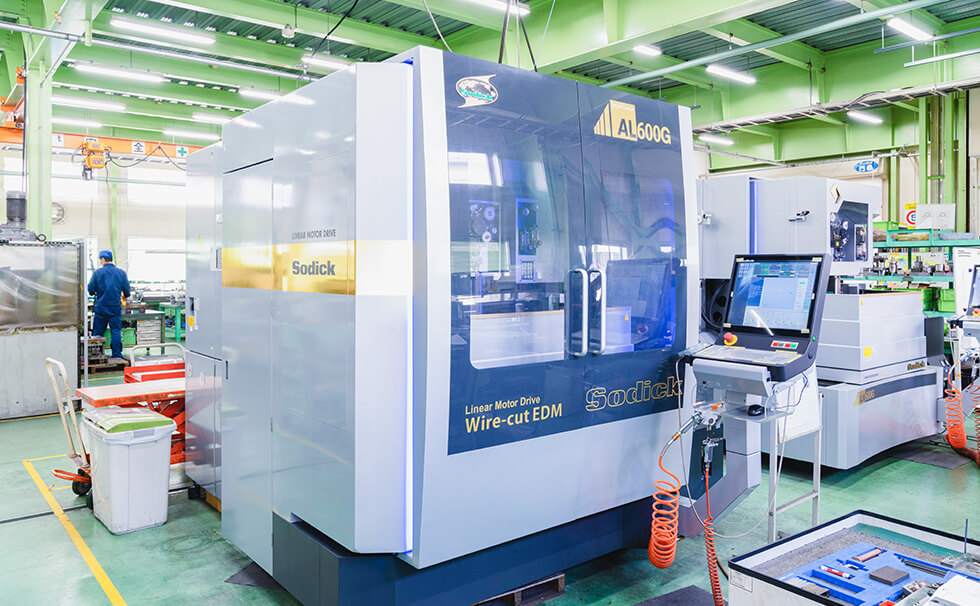
ワイヤーカット放電加工機(SODIC)
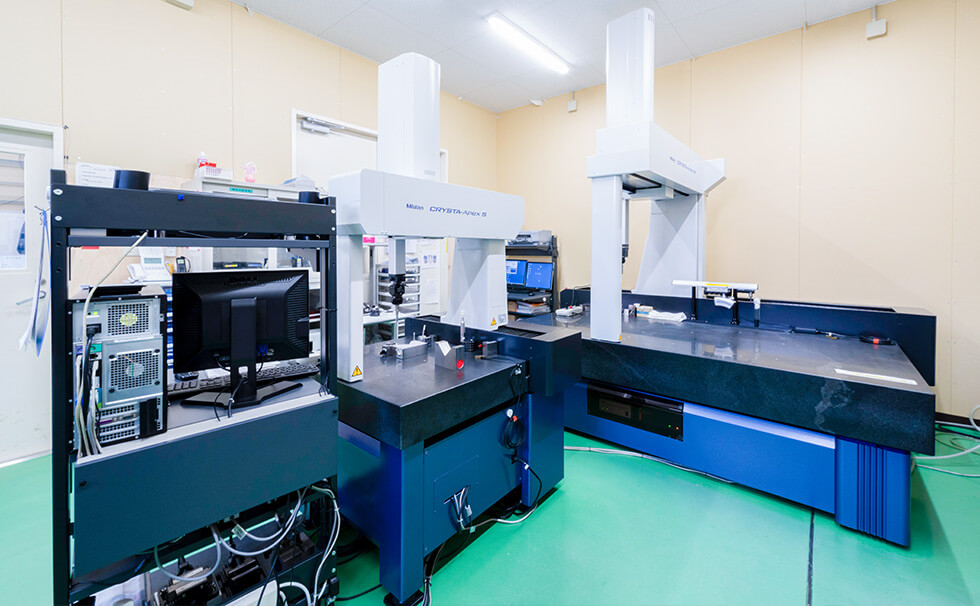
自動三次元測定器(ミツトヨ)
生産性を向上させる、プレス周辺自動設備も自社製です
スポット溶接機や自動検査機など、自社で製作した自動機を積極的に投入。作業者数を減らすことによるコスト削減だけでなく、さらなる生産性の向上、品質の安定化を図っています。また、社内でのメンテナンスが可能なので、ラインの安定稼働も実現しています。
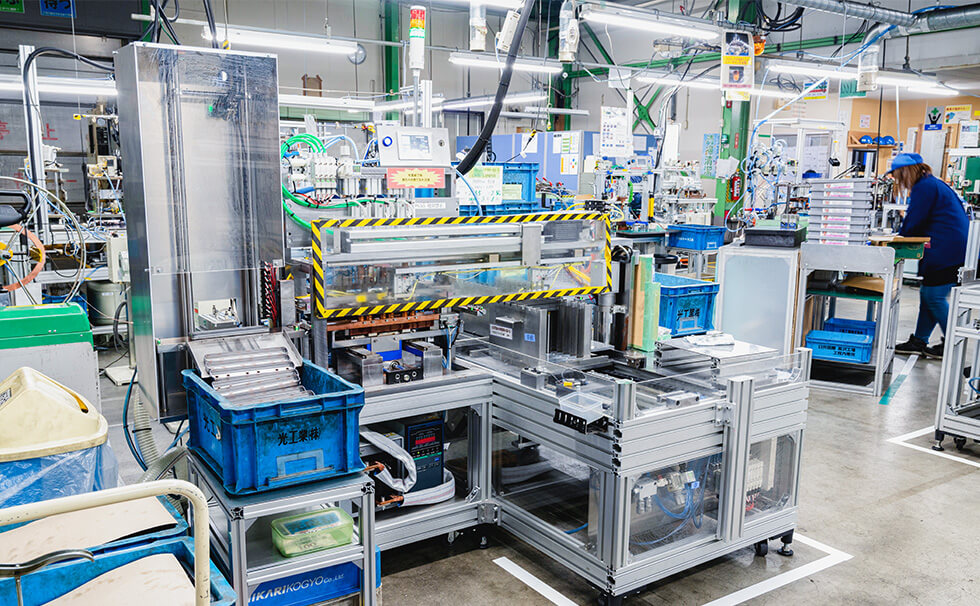
スポット溶接機
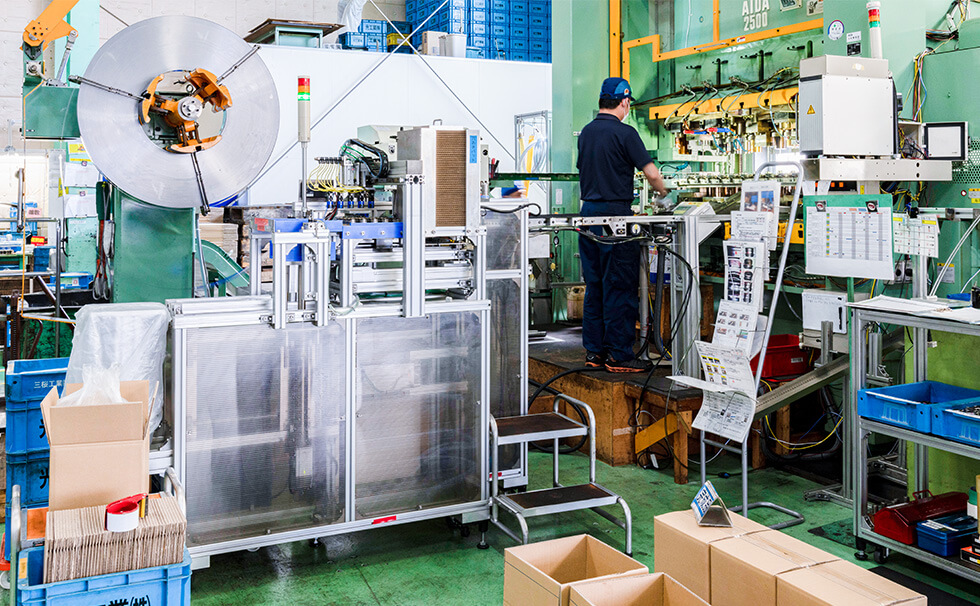
オーリングジョイント
寸法検査・整列機
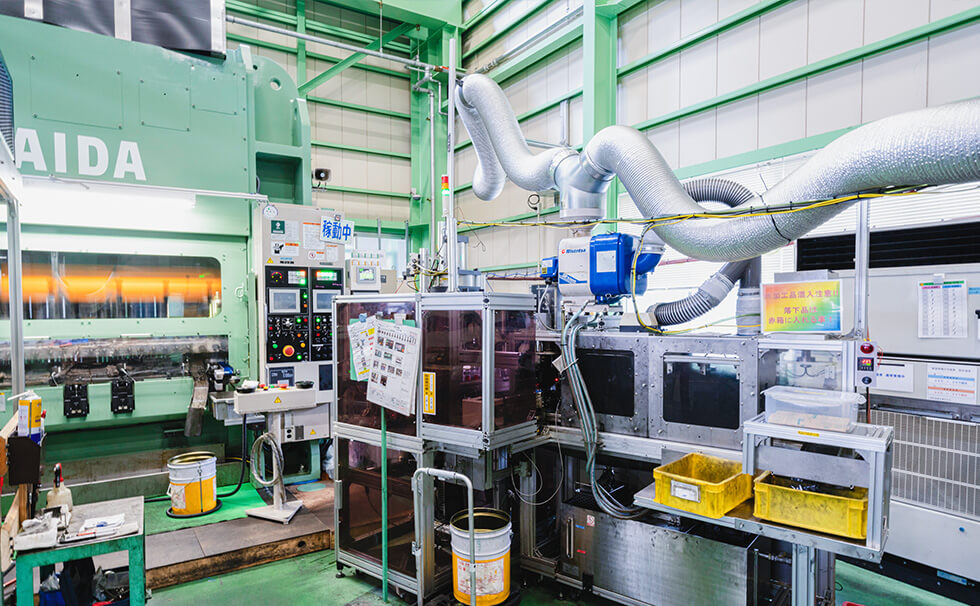
プレスカップライン洗浄機 兼
横穴加工機
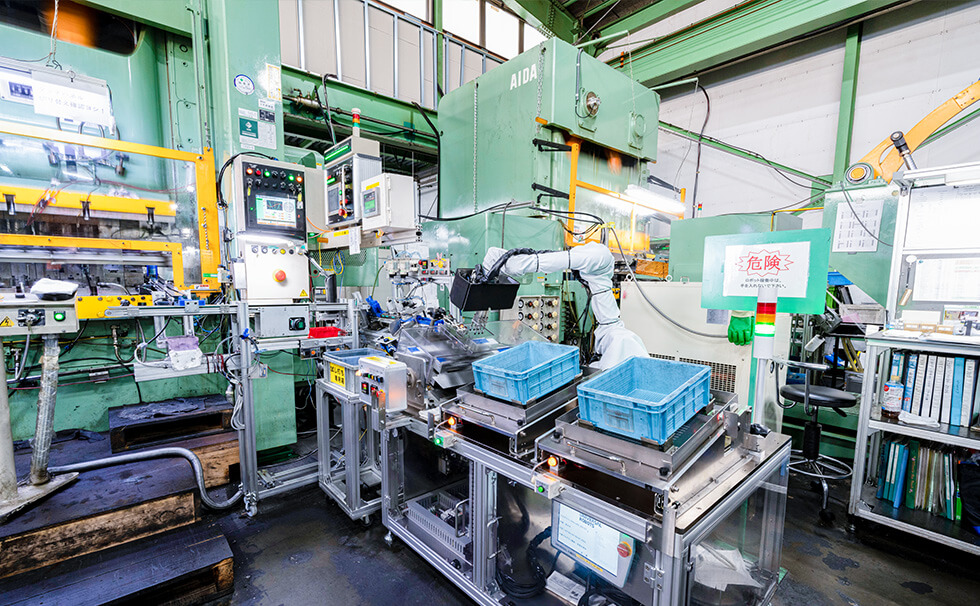
枝管寸法検査・自動整列機
INTEGRATED PRODUCTION SYSTEM一貫生産体制
技術の進歩、時代のニーズ、お客様の経営環境など、ものづくり取り巻く様々な変化に柔軟に対応し、期待以上の成果を上げるために、当社では仕様のお打ち合わせから出荷までを責任持って行う一貫生産体制を構築。多品種少量から大量生産まで、多様なご要望にお応えできる環境を整えています。
金型作りからプレス加工、品質検査まで、安心の一貫生産体制
1.お打合せ
どのような製品を作りたいのか、お客様のニーズを詳細にヒアリング。「他社では断られた」「プレス加工の前例がない」といった案件も多く持ち込まれます。
2.金型設計・製作
金型製作は光工業の技術の要。経験に裏打ちされたアイデアが盛り込まれた設計を、確かな技術と最新の設備で具現化することにより、優れた金型が生まれます。
3.プレス加工
「プレス機と金型さえあれば、誰が加工しても同じ」ではありません。近年増えつつある難加工製品の安定的な量産には、長年のノウハウと充実した設備が必須です。
4.洗浄
2台の汎用洗浄機を保有しているので、製品の洗浄対応も可能です。また、生産数の多い製品については、自作の洗浄機によるライン内洗浄も行っています。
5.サブアッシー
お客様のご要望に応じて、スポット溶接やカシメなどの仮組対応まで承っています。自作の組立機や治具を駆使し、効率的な生産体制で対応します。
6.検査
室温管理された検査室を完備。3台の三次元測定機や真円度測定機をはじめとする最新の検査機器を駆使し、専任の検査員が精密な検査測定を行います。
7.出荷
効率化・迅速化を実現するため、自社工場内に自動倉庫を保有。月間で約2000種類にも及ぶ製品を正確に把握し、スムーズに出荷できるシステムを整えています。